- KDDI HOME
Corporate Information
Sustainability
Risk Management and Internal Controls
Risk Management and Internal Controls
KDDI's Approach (Risk Management and Internal Control)
In the ever-changing business environment, the risks that companies face are increasingly diverse and complicated.
Based on the Companies Act, we have resolved the "Basic Policy for Constructing an Internal Control System" at the board of directors and have established and operated an internal control system, including a risk management structure, in accordance with this policy. We define factors and events that negatively influence the achievement of our business goals as risks and consider enforcing risk management as a material business challenge. In order to be sustainable and responsible to society, we promote risk management initiatives throughout the KDDI Group.
KDDI's Risk Management and Internal Control
We have established a system to centralize the management of risks with the Corporate Sector.
Furthermore, we are promoting risk management throughout the KDDI Group, in order to realize the continuous growth of the entire group. We have appointed 44 Internal Control System Managers within KDDI and 47 at group companies, as well as 7 Internal Control System Directors to oversee their activities.
Under their leadership, we introduce and run internal control systems, carrying out risk management activities and run operational quality improvement activities to foster a company culture in which risks are less likely to arise.
Personnel in Charge of Internal Control

Risk Management Activity Cycle
In order to prevent critical events for the company, we at KDDI consider that it is important to recognize signs of danger and implement preventive measures before the situation worsens. Based on this idea, we follow the PDCA cycle for risk management. We also have an organizational framework for risk management in place to ensure any risks we find will be addressed promptly and appropriately.
PDCA cycle
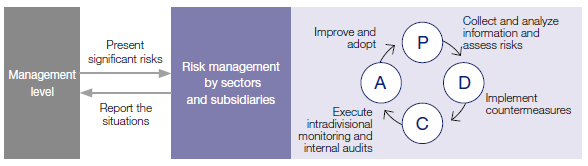
Risk Identifying Process
We conduct risk information investigations at least once a year to identify significant risks that seriously influence corporations and discuss measures to reduce such risks and their impacts as much as possible in case we face them.
In order to ensure the achievement of our business goals, in FISCAL 2023, we selected 23 significant risks based on issues that manifested in the past and changes in the business environment, and held internal audits centered on risk prediction, the reduction of significant risks and risk approach. The status of these significant risks is also reflected on business risks that are revealed in the Securities Report since it relates to the finance as well.
Initiatives in Response to the Internal Control Reporting System (J-SOX)
In response to the internal control reporting system based on the Financial Instruments and Exchange Law implemented since fiscal year 2008, we conducted evaluations of the internal controls at KDDI and major group companies both in Japan and overseas to ensure the reliability of financial reporting. The results of these evaluations are compiled into internal control reports and disclosed to investors.
Activities to Enhance Operational Quality
We have established a Promotion Office to enhance the overall operational quality activities of the entire company within the Corporate sector. Each division's Internal Control System Manager serves as the Promotion Officer, autonomously working to improve the quality of operations while aiming for operational efficiency and standardization. The initiatives resulting from these operational quality improvement activities are shared company-wide, and mechanisms are in place for all employees to utilize them to enhance the quality of operations in their respective divisions.
Furthermore, to further raise awareness and motivation regarding the quality of operations among employees, we have introduced the Best Award to recognize excellent and ambitious initiatives.
Activities to Enhance Operational Quality
- Setting and sharing autonomous goals and promotion plans for each division.
- Implementation of the Best Award recognition for outstanding operational quality improvement activities.
- Conducting an awareness survey questionnaire for operational quality improvement activities.
- Sustainability
-
- Environment
- Society
- Governance
- Mid-Term Sustainability Targets
- CEO Message
- KDDI's Commitment to Sustainability
- KDDI's SDGs
- Integrated Sustainability and Financial Report
- ESG data
- Compliance
- Community Cooperation (in Japanese only)
- Social Contribution Activities
- Sustainability News (in Japanese only)
- External Recognition/Initiatives
- Recommended Contents
-